Dans les industries métallurgiques, le moulage sous pression en chambre chaude a connu une hausse significative allant jusqu’à 8 % en raison de sa viabilité rapide et économique sur le marché mondial. Le processus reproduit des pièces complexes et détaillées de haute qualité avec un délai d’exécution minimal. De plus, il offre des avantages économiques lorsqu’il est utilisé pour des lots de grande quantité. Le processus de moulage sous pression en chambre chaude est reconnu pour sa précision, son exactitude et ses pièces aux performances optimales en raison de l’intégration de systèmes CNC dans la conception des configurations de pièces. Par conséquent, de l’automobile et de l’aérospatiale aux produits de consommation, son rôle est vital lorsque des pièces aux spécifications exactes sont cruciales. De plus, il s’agit d’un processus de fabrication relativement bon marché et fastidieux, contrairement à d’autres techniques conventionnelles.
Qu’est-ce que le moulage sous pression en chambre chaude ?
Par rapport aux méthodes de moulage conventionnelles, le moulage sous pression à chambre chaude suit le même mécanisme. Il consiste à placer du métal en fusion dans la cavité du moule. Ensuite, une injection à haute pression est insérée qui transforme rapidement le métal en fusion en forme de moule (ce qui entraîne la forme de la pièce souhaitée) lors de la solidification.
Ce cycle se répète jusqu’à ce que vous atteigniez le volume de pièces souhaité. Étant donné que le moulage sous pression en chambre chaude est utilisé de manière optimale pour les basses températures de fusion, un four et un réglage de matrice sont donc nécessaires pour ce processus spécialisé. Contrairement au moulage sous pression en chambre froide , ce four est construit à l’intérieur et équipé d’une machine de moulage sous pression. Avant d’entrer dans les détails du processus, il est nécessaire de comprendre les exigences d’assemblage pour le processus de moulage sous pression en chambre chaude. Fondamentalement, une machine de moulage sous pression se compose de six parties, dont :
Four de chauffage
Le four de chauffage est un élément fondamental qui permet de faire fondre le métal brut solide en une forme liquéfiée. Il est spécialement conçu pour permettre des températures élevées afin d’éviter un refroidissement prématuré de l’alliage prévu.
Col de cygne
Le col de cygne sert de passage pour assurer une transition en douceur du métal en fusion vers la matrice. En d’autres termes, on peut dire qu’il comble l’écart entre la ligne d’alimentation et le mécanisme d’injection. Il est généralement fabriqué à partir de quatre métaux durables comme l’acier moulé ou forgé. De plus, ce composant est toujours immergé dans le bain de métal en fusion pour résister aux impacts thermiques pendant l’opération de coulée. Les fabricants doivent compter sur le remplacement des cols de cygne dans des conditions de forte usure lors de grandes séries de production.
Ajutage
Comme son nom l’indique, la buse est responsable de la régulation en douceur du métal coulé dans la matrice en appliquant un gaz à haute pression. Pendant ce temps, le col de cygne joue un rôle de passerelle pour assurer une transition en douceur dans le mécanisme d’écoulement.
Piston hydraulique
Un piston hydraulique est principalement utilisé pour maintenir une pression élevée dans la matrice en utilisant du gaz ou de l’huile de lubrification comme source d’énergie. Le piston a tendance à se déplacer vers le haut et vers le bas. Le mouvement ascendant du piston plongeur laisse le métal en fusion pénétrer dans la chambre chaude, puis le mouvement descendant du piston se transforme en la configuration souhaitée.
Système de moulage
Enfin, voici le système de moulage lui-même. Un système de moulage est composé de deux parties identiques : la cavité et l’éjecteur. En règle générale, le moule utilisé dans la coulée sous pression en chambre chaude est en acier comme dans les autres procédés de moulage.
Éjection
L’éjection est la phase finale du processus de moulage en chambre chaude. Les opérateurs retirent mécaniquement la pièce moulée en s’assurant de son intégrité et la refroidissent pour la rendre solide. Après une éjection réussie, les pièces moulées peuvent encore subir d’autres traitements de post-traitement. Parmi les processus de finition les plus courants, on trouve : l’anodisation, le polissage et la peinture.
Procédé de moulage sous pression en chambre chaude : guide étape par étape
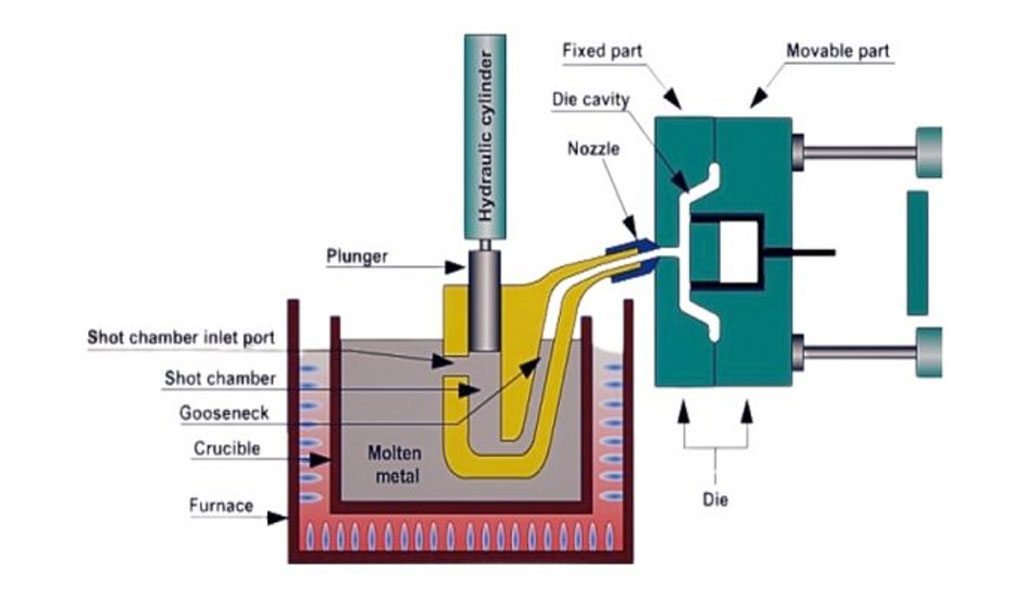
Le succès du processus peut être assuré par une familiarisation complète. Voici un guide étape par étape du processus de moulage sous pression en chambre chaude :
Étape 1. Fusion de l’alliage métallique
L’étape initiale consiste à faire fondre l’alliage, notamment le zinc ou le magnésium, dans un four qui comprend une chambre de combustion pour brûler le combustible et faire fondre l’alliage métallique souhaité. La température optimale requise est d’environ 1220°F à 6152°F selon les propriétés du métal utilisé.
Étape 2. Injection
Ensuite, le métal liquide est placé uniformément à l’intérieur d’une matrice lubrifiée en soulevant le piston. Ici, un creuset est utilisé pour l’injection fine du métal en fusion afin d’éviter tout problème de débordement. Après cela, la matrice est fermée pour la phase suivante.
Étape 3. Application d’une pression élevée
Cette étape a pour but de transformer le métal liquide en la forme souhaitée en appliquant une pression élevée, généralement comprise entre 5 et 35 MPa à travers le piston . Cette étape détermine le résultat du processus. Par conséquent, les fabricants doivent s’assurer qu’il n’y a pas de trou perforant à l’intérieur de la cavité du moule pour éviter tout risque de rétrécissement des pièces.
Étape 4. Éjection et solidification
La forme est ensuite refroidie et le produit est éjecté hors de la cavité du moule. Ce produit moulé sous pression est ensuite inspecté pour détecter tout défaut afin de garantir sa qualité. Parallèlement, le cycle se répète selon les étapes susmentionnées.
Métaux utilisés dans la coulée sous pression en chambre chaude
Comme mentionné ci-dessus, le procédé de moulage sous pression en chambre chaude est adapté aux métaux à bas point de fusion. De cette façon, le zinc et le magnésium sont particulièrement utilisés pour les applications de moulage. Examinons les aspects critiques de ces métaux dans le tableau ci-dessous.
Tableau : Caractéristiques des métaux compatibles pour le HCDC
Métal | Densité (g/cm³) | Température de fusion (°C) | Aspects de compatibilité |
Zn | 7.14 | 419-426 | Convient en raison de son point de fusion modéré et de sa bonne fluidité, |
Mg | 1.738 | 650-700 | Excellent en raison de sa faible température de fusion, de sa bonne fluidité et de l’usure minimale de la matrice |
Pb | 11.34 | 327,5 | Bon en raison de sa faible température de fusion et de sa fluidité modérée, adapté à des applications spécifiques |
Zinc
Le zinc est avant tout un métal dont le point de fusion est extrêmement bas (419 °C). Sa légèreté, sa grande résistance, sa capacité à résister à la corrosion et sa grande fluidité en font un choix idéal pour les applications de moulage sous pression. De plus, c’est un alliage relativement moins cher que le magnésium et le plomb. De plus, le zinc possède des caractéristiques remarquables telles que la dureté et la résistance à l’usure. Cette capacité permet au zinc de supporter des conditions difficiles. Le zinc permet de résoudre les problèmes de faible porosité dans le processus de moulage sous pression.
Magnésium
Le magnésium est un métal de premier choix pour la coulée sous pression en chambre chaude. Il est léger, résistant, thermiquement stable et recyclable avec une densité de 1,7 g/cm³ . Le magnésium est chimiquement résistant et surtout l’alliage le plus facile à couler. De plus, il possède des capacités de blindage élevées pour résister aux radiofréquences et aux interférences électromagnétiques. Comme le zinc, le magnésium présente moins de risques de porosité et moins de capacités oxydantes. Par conséquent, il est utilisé dans les domaines de l’automobile, de l’aérospatiale et des appareils électroniques.
Plomb
Le plomb présente une aptitude remarquable au moulage, une capacité de réduction de poids et un point de fusion bas qui en font un candidat compatible pour les applications de moulage. Il se distingue des autres alliages en raison de sa malléabilité, de sa ductilité et de sa capacité à répondre aux exigences strictes et exactes des pièces pour les produits à usage industriel.
Avantages du moulage sous pression à chambre chaude
Voici quelques-uns des avantages les plus courants du moulage sous pression en chambre chaude.
- Le cycle de production du procédé de moulage sous pression à chambre chaude est relativement plus rapide que celui des autres méthodes conventionnelles. En moyenne, il peut traiter 15 cycles par minute.
- Le moulage sous pression en chambre chaude permet de réaliser des produits de forme sophistiquée avec une relative facilité, et les pièces nécessitent des précisions dimensionnelles élevées.
- Le procédé est très économique lorsqu’il s’agit de volumes en vrac.
- La fabrication de pièces en moulage sous pression en chambre chaude n’est pas complexe contrairement au moulage par précision et au moulage sous pression par gravité .
- Le coût de maintenance est relativement faible par rapport au moulage sous pression en chambre froide (voir plus d’informations sur le moulage sous pression en chambre chaude par rapport au moulage sous pression en chambre froide). En effet, le transfert direct de l’alliage est effectué pendant le processus pour atténuer les risques potentiels de porosité et de retrait.
- Les fabricants de produits bénéficient du processus de mise en forme de pièces avec des tolérances plus strictes, des dimensions précises et des finitions de texture lisse avec des exigences de post-traitement minimales.
- Les pièces fabriquées par moulage sous pression en chambre chaude possèdent une résistance supérieure jusqu’à 25 à 30 % à celle du moulage au sable.
- Un moule de moulage sous pression présente une polyvalence dans la mesure où il permet d’utiliser plusieurs cavités dans un seul moule.
- La durée de vie des outils utilisés dans le moulage sous pression en chambre chaude est souvent longue, en raison des exigences de basse température pour la fabrication des pièces.
Inconvénients du moulage sous pression en chambre chaude
Certains des inconvénients du moulage sous pression en chambre chaude comprennent :
- Le moulage sous pression en chambre chaude est limité aux métaux non ferreux à basse température de fusion.
- Les risques de porosité, de bavures et de formation de cloques sur les pièces sont plus élevés dans le moulage sous pression en chambre chaude par rapport aux autres techniques de moulage.
- Plus le volume de production est faible, plus le coût amorti par pièce est élevé. Cela signifie que le moulage sous pression en chambre chaude est efficace et économique pour produire des pièces en grande quantité.
- Le coût des services publics et des auxiliaires utilisés, par exemple les fours, les moules et les matrices, entraîne des dépenses initiales élevées pour le projet.
- Le moulage sous pression en chambre chaude est un processus à forte intensité de main-d’œuvre.
Conseils pour choisir le procédé de moulage sous pression en chambre chaude
Il y a plusieurs facteurs à prendre en compte lors de la sélection d’un procédé de moulage sous pression à chambre chaude pour vos projets. Voici quelques conseils d’experts qui vous aideront à faire un choix judicieux de procédé :
- Alliage de moulage sous pression : l’applicabilité du procédé repose sur des matériaux à faible point de fusion. En général, le procédé de moulage en chambre chaude est privilégié pour le zinc, le plomb, l’étain et le magnésium. Ces alliages ont des températures de fusion minimales inférieures à 600 °C. Par conséquent, les fabricants OEM doivent connaître les propriétés des alliages de moulage avant de lancer des projets de moulage sous pression.
- Complexité des pièces : En règle générale, les fabricants ont l’intention d’utiliser le moulage sous pression en chambre chaude pour les produits moins complexes. Les pièces de formes cylindriques et radiales peuvent être fabriquées à l’aide d’un équipement de moulage sous pression en chambre froide verticale. Il est donc indispensable de connaître les spécifications des pièces pour tirer le meilleur parti du processus.
- Considérations relatives aux coûts : évaluez les coûts globaux du processus, notamment les frais d’outillage, d’équipement, de matériaux et de main-d’œuvre. La coulée en chambre chaude est souvent efficace pour les grandes séries. L’analyse des coûts du projet dépend principalement du volume, du budget, de la configuration de l’usinage et du délai.
- Exigences de finition : La finition de surface optimale est un autre facteur à prendre en compte. Si vous êtes plus préoccupé par les pièces avec des textures de finition plus élevées, optez pour le moulage sous pression en chambre chaude. Il produit généralement des pièces avec une finition de surface lisse.
- Demandez l’avis d’un expert : la mise en œuvre réussie du processus exige que certains éléments soient pris en compte, par exemple le budget, le calendrier, les spécifications de conception et plusieurs autres éléments. Par conséquent, il est toujours recommandé de consulter un expert comme CFS Foundry pour faire un choix judicieux en fonction des exigences de votre projet.
Applications du moulage sous pression en chambre chaude
Comme nous l’avons vu, le moulage sous pression en chambre chaude produit des pièces fiables avec une durabilité exceptionnelle et une finition de surface soignée. Des pièces automobiles aux composants d’avion, il joue un rôle clé dans la fabrication de pièces pour répondre aux exigences de l’industrie. Découvrons quelques-unes des applications de cette technique dans les secteurs de fabrication.
Industrie automobile
L’industrie automobile est le principal consommateur de pièces moulées sous pression. Les produits moulés fabriqués par moulage sous pression en chambre chaude sont largement utilisés dans les composants intérieurs et extérieurs des automobiles pour améliorer les performances optimales et la maniabilité. Quelques exemples incluent : les boîtes de vitesses, les boîtiers, les carters, les blocs moteurs et les véhicules de loisirs.
Électronique grand public
Le moulage sous pression en chambre chaude joue un rôle central dans la fabrication de pièces destinées aux industries électroniques. Sa résistance élevée et sa précision dimensionnelle sont des caractéristiques clés qui lui permettent d’être utilisé dans des appareils tels que les smartphones, les ordinateurs portables et les gadgets pratiques.
Dispositifs médicaux
Les pièces robustes et très durables sont des besoins fondamentaux du secteur de la santé. Ainsi, les pièces moulées en chambre chaude jouent un rôle important dans la création de boîtiers et de boîtiers d’appareils de diagnostic. Parmi les exemples courants, citons : les dispositifs médicaux implantables et les composants de seringues.
Industrie aérospatiale
Dans l’industrie aérospatiale, le moulage sous pression en chambre chaude permet de fabriquer des pièces solides mais légères pour améliorer la fonctionnalité et les performances globales des composants d’aéronefs. Il facilite la production de pièces pour les moteurs à réaction, les trains d’atterrissage et les pièces axées sur l’intégrité structurelle. De plus, les pièces présentant des caractéristiques détaillées sont plus faciles à réaliser grâce à ce processus incroyable.
Fabrication industrielle
Les secteurs manufacturiers dépendent fortement du procédé de moulage sous pression en chambre chaude. Le procédé permet de créer des outils et des matrices pour le moulage par injection. De plus, le matériel, les biens de consommation et les pièces de télécommunication comme les antennes peuvent être moulés par moulage sous pression en chambre chaude.
Contactez CFS Foundry pour des services de moulage sous pression en chambre chaude :
Chez CFS Foundry, avec une décennie d’expérience dans le moulage sous pression , nos experts techniques s’engagent à apporter prééminence et fiabilité à votre projet envisagé.
Nos ingénieurs vous aident à réaliser des analyses DFM, à sélectionner judicieusement le matériau de moulage et à réaliser le processus en garantissant une qualité élevée et le meilleur service client. Nous possédons des équipements d’usinage de pointe équipés par des professionnels expérimentés pour rendre vos pièces pratiques dans un délai court.
De plus, nous proposons des services de moulage pour un large éventail de clients. Que vous ayez besoin de pièces complexes de volumes moyens à grands, nous avons la capacité de répondre à des spécifications et des exigences précises dans le cadre de votre budget abordable.
Pour toute demande de renseignements ou pour discuter de votre projet de moulage sous pression, n’hésitez pas à nous envoyer vos dessins à [email protected]. Nos ingénieurs analyseront votre conception et vous fourniront un devis instantané avec une assistance du début à la fin.
FAQ
Q1. L’aluminium peut-il être coulé par moulage sous pression en chambre chaude ?
En règle générale, le moulage sous pression en aluminium n’est pas compatible avec le moulage sous pression en chambre chaude car il présente un point de fusion très élevé de 660 °C. Normalement, l’adéquation du métal dépend de ses caractéristiques thermiques. Par conséquent, en raison de la température de fusion plus élevée, l’aluminium peut présenter un risque d’endommager les composants de la machine tels que le col de cygne et la buse.
Q2. Quelle est la principale différence entre le moulage sous pression en chambre chaude et en chambre froide ?
La différence fondamentale réside dans la compatibilité des matériaux. Par exemple, les métaux ayant des points de fusion plus élevés, supérieurs à 600 °C, tels que l’aluminium, le cuivre et le laiton, sont susceptibles d’être coulés dans des machines de coulée sous pression à chambre froide. En revanche, les métaux ayant des points de fusion plus bas sont coulés dans le cadre du processus de coulée à chambre chaude. En outre, d’autres facteurs, tels que la configuration de l’usinage ou de l’assemblage, les spécifications des pièces, le temps de cycle et le volume prévu, jouent un rôle clé.
Q3. Existe-t-il des alternatives au procédé de moulage sous pression en chambre chaude ?
Oui, il existe plusieurs alternatives parmi lesquelles choisir. Le choix final dépend de la conception et de la complexité de votre produit. Voici quelques procédés de moulage couramment utilisés :
- Moulage par cire perdue
- Moulage sous pression en chambre froide
- Coulée sous pression par gravité