Lorsque nous parlons de production de pièces métalliques, la première chose que nous prenons en compte est la précision et l’efficacité du processus. Le moulage sous pression en chambre froide y joue un rôle important. Il offre une méthode fiable pour produire des pièces métalliques complexes avec une grande précision. Explorons donc son processus étape par étape, ainsi que ses nombreux avantages et applications.
Qu’est-ce que le moulage sous pression en chambre froide ?
Le moulage sous pression en chambre est une forme de moulage sous pression. Ce procédé est utilisé pour produire des pièces métalliques de haute qualité aux formes et géométries complexes. Au cours de ce procédé, le métal en fusion est injecté dans le moule en acier. Cette opération est généralement réalisée sous haute pression pour créer un composant précis. Le moulage sous pression comporte deux méthodes : le moulage sous pression en chambre froide et le moulage sous pression en chambre chaude . Le moulage sous pression en chambre froide dispose d’un four à creuset séparé qui est utilisé pour faire fondre le métal avant de le transférer vers le mécanisme d’injection.
Procédé de moulage sous pression en chambre froide : étape par étape
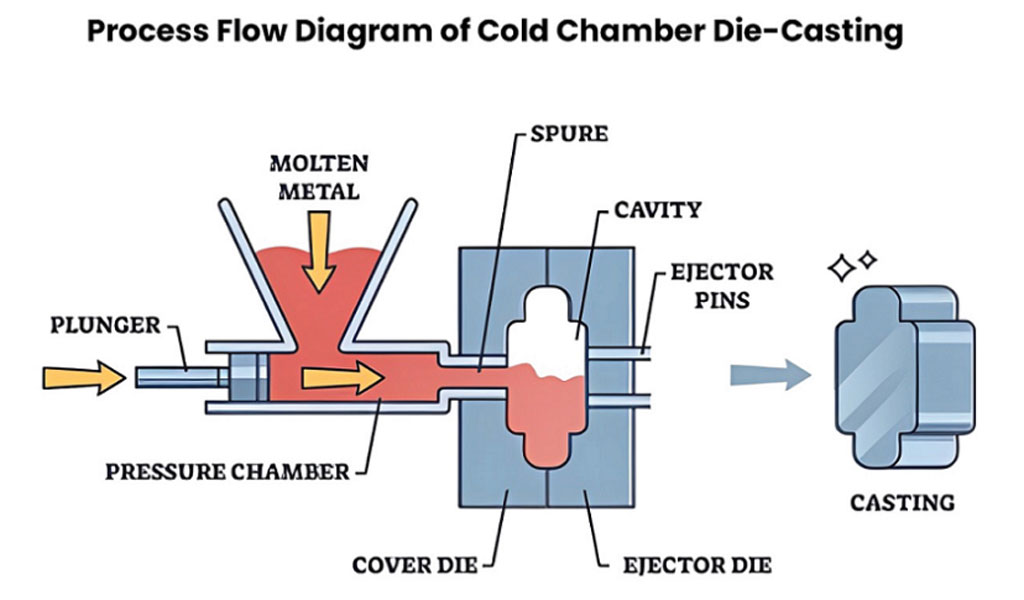
Étape 1. Préparation du moule
Le moulage sous pression en chambre froide commence par la préparation du moule. Il est généralement composé d’acier trempé et de matériaux durables. De plus, le moule est conçu pour correspondre aux spécifications exactes des pièces métalliques. Mais avant cela, les processus suivants sont effectués.
- Conception de pièces métalliques : La première étape du moulage sous pression en chambre froide est la préparation du moule. Mais avant cela, les ingénieurs créent un modèle CAO détaillé des pièces métalliques. Ces modèles sont ensuite utilisés pour concevoir le moule. Certains facteurs doivent donc être pris en compte au cours de ce processus, tels que la géométrie des pièces métalliques, les angles de dépouille et les systèmes de contrôle.
- Outillage : Après avoir conçu les pièces métalliques, des ingénieurs qualifiés créent le moule à l’aide d’un usinage CNC ou d’autres techniques de fabrication. Ce moule se compose généralement de deux moitiés telles que la cavité et la partie froide. Ces moitiés fonctionnent ensuite ensemble pour créer la forme de pièce souhaitée.
- Finition de surface : Une fois le moule créé, il est essentiel de lui donner une finition appropriée. Ainsi, vous pouvez obtenir la texture et les finitions de surface souhaitées sur la pièce finale. Il existe certaines techniques que vous pouvez utiliser pour la finition de surface, à savoir le polissage ou la gravure du grain.
Étape 2. Faire fondre le métal
La deuxième étape est la fusion du métal. Au cours de ce processus, le métal coulé est injecté dans un four séparé. Ces métaux peuvent être des alliages d’aluminium, de magnésium ou de cuivre. Les métaux fondent alors jusqu’à leur forme liquide. Ensuite, ces métaux fondus sont transférés dans une machine à chambre froide. Voyons donc chaque étape de ce processus dans l’ordre.
- Fonctionnement du four : Les alliages métalliques sont chauffés dans un four jusqu’à leur point de fusion. Le four est ensuite spécialement conçu pour faire fondre les métaux. Cela peut utiliser une résistance électrique, un gaz de frappe pour les brûleurs ou un chauffage par induction. Obtenez la température de silence.
- Alliage : Ici, nous ajoutons des alliages aux métaux en fusion. Ce procédé peut aider à obtenir des propriétés mécaniques optimales avec une composition chimique appropriée.
- Dégazage et fluxage : À ce stade, les impuretés et les gaz sont d’abord éliminés des gaz en fusion. Cette opération est généralement réalisée à l’aide d’agents de dégazage et de fluxage. Ce processus nous aide à améliorer la qualité et l’intégrité de la pièce moulée finale.
Étape 3. Transfert du métal vers la machine à chambre froide
Ici, nous transférons le métal en fusion dans une machine de coulée sous pression à chambre froide. Cette machine comprend une chambre froide. Ici, nous stockons le métal en fusion pendant une courte durée. Ensuite, nous livrons le métal au moule. Cette chambre froide aide les métaux modernes à se séparer du système d’injection. De plus, elle empêche la solidification prématurée. Elle permet la coulée de métal à point de fusion élevé. Ainsi, les étapes incluses dans ce processus sont les suivantes :
- Coulée ou louche : Lorsque le métal atteint la température et la composition souhaitées, on le transfère vers la machine de coulée sous pression à chambre froide. Cette opération se fait généralement à l’aide de louches ou d’un système de coulée. Ce système transporte le métal en fusion du four jusqu’au creuset de maintien de la machine.
- Conception du creuset : La machine à chambre froide comprend un creuset ou un réservoir. Il retient efficacement le métal en fusion. Cette chambre est spécialement conçue pour supporter des températures et des pressions élevées pendant le processus d’injection. De plus, elle valide le transfert de métal de manière sûre et efficace.
Étape 4. Injection dans le manchon d’injection
Ce cycle commence lors de la fermeture de la séquence d’initiation moderne de l’injection. Au cours de ce processus, un piston hydraulique applique une pression élevée sur le métal moderne et le force vers les esclaves courts. De plus, la pression exercée sur le métal permet un écoulement rapide et une distribution uniforme dans la cavité. Voici donc les détails de ce processus :
- Système de grenaille : Il peut s’agir d’un système de grenaille. Ici, la machine de moulage sous pression à chambre froide est équipée d’un système hydraulique. Il contrôle le processus d’injection. Ainsi, le piston applique une pression sur le métal en fusion dans une chambre froide et le force dans les manchons de grenaille.
- Contrôle de la pression : Ici, nous contrôlons soigneusement la pression d’injection. Ainsi, nous pouvons optimiser le flux de métal. De plus, la cavité du moule est remplie uniformément tout au long du processus. Les capteurs de pression et les mécanismes de rétroaction permettent un contrôle précis du processus d’injection. Cela minimise les défauts et assure une qualité constante des pièces métalliques.
Étape 5. Injection dans le moule
Ainsi, lorsque le métal en fusion pénètre dans un manchon de coulée, il est ensuite déplacé vers la cavité du moule à travers des portes et des buses, sous pression. De plus, ce métal en fusion déplace l’air et le gaz présents à l’intérieur de la cavité du moule. Il remplit également les détails complexes du moule. Ce processus comprend :
- Conception de la porte : Les manchons de coulée transfèrent le métal en fusion vers la cavité du moule. Ils utilisent un système de glissières, de portes et d’épicéas. De plus, la conception de ce système de porte est très importante pour contrôler le flux de métal. De plus, il minimise les turbulences et empêche également l’emprisonnement d’air à l’intérieur de la cavité du moule.
- Remplissage du moule : lorsque le métal en fusion pénètre dans la cavité du moule, il remplit rapidement les espaces. De plus, il libère de l’air et remplit les détails complexes du moule. Ainsi, dans ce cas, des conceptions de ventilation et de distribution appropriées contribuent à un écoulement fluide du métal. De plus, elles évitent les défauts tels que les poches d’air.
Étape 6. Refroidissement et solidification
Après avoir été injecté dans la cavité du moule, le métal commence à refroidir et à se solidifier. Il prend la forme précise du moule. La vitesse de refroidissement permet de contrôler les risques de défauts internes. Voici donc quelques étapes du refroidissement et de la solidification.
- Canaux de refroidissement . Le moule est équipé de canaux ou circuits de refroidissement. Ces circuits permettent de faire circuler le liquide de refroidissement, c’est-à-dire l’eau, qui sert à évacuer la chaleur du métal en fusion. De plus, ces canaux permettent de réguler la vitesse de refroidissement. Ils favorisent la solidification uniforme de la pièce moulée tout au long du processus.
- Contrôle de la solidification. Les fabricants optimisent le processus de solidification en contrôlant la température et le débit du liquide de refroidissement. Cela les aide à minimiser la porosité, le retrait et les défauts internes de la pièce moulée.
3. Temps de cycle. Le temps de cycle est la partie la plus longue de la phase de refroidissement et de solidification. Ce sont les stratégies de refroidissement efficaces qui permettent aux conceptions de moules de réduire le temps de cycle. De plus, cela augmente le débit de production.
Étape 7. Éjection des pièces métalliques
Une fois que le métal a suffisamment refroidi et s’est solidifié, il sort de la cavité du moule. Certaines broches et mécanismes d’éjection sont utilisés pour libérer la pièce. Voici donc quelques étapes du processus d’éjection :
- Ouverture du moule : Lorsque la pièce est correctement solidifiée, le moule s’ouvre et libère la pièce. Dans ce cas, un système hydraulique ou mécanique actionne les deux moitiés du moule. Il leur permet de se séparer et d’exposer ainsi la pièce finie.
- Mécanisme d’éjection : Ici, la pièce moulée est éjectée de la cavité du moule grâce aux broches ou aux plaques d’éjection. Ces broches sont situées à l’intérieur de la cavité du moule. Assurez-vous donc que ce mécanisme est soigneusement conçu et positionné afin d’éviter tout dommage lors de la coulée.
Étape 8. Découpe et finition
Une fois la pièce éjectée du moule, la dernière étape est le découpage et la finition. L’excédent de matière, c’est-à-dire les bavures, est coupé de la pièce métallique. Cette opération est généralement réalisée à l’aide d’outils de découpe ou de matrices de découpage. Voici donc quelques étapes à suivre :
- Élimination des bavures : à cette étape, les fabricants utilisent des outils de coupe, des matrices de découpe ou un usinage CNC pour éliminer l’excès de matière attaché à la pièce moulée. Cette étape est généralement réalisée pour s’assurer que la pièce finale respecte la tolérance dimensionnelle.
- Traitement de surface : Cela dépend des spécifications et des applications du client. Le traitement de surface, tel que le grenaillage, la finition vibratoire ou le revêtement par poudre, peut être appliqué à la pièce moulée. Cela est généralement fait pour améliorer l’apparence et la fonctionnalité de la pièce moulée.
- Contrôle et inspection qualité : Une fois la pièce terminée, elle est soumise à un contrôle précis à l’aide de jauges dimensionnelles. D’autres méthodes d’inspection peuvent être utilisées, telles que les machines de mesure de coordination (MMT) et les techniques d’inspection visuelle. Ces techniques permettent de vérifier les spécifications de conception et les normes de qualité.
Métaux utilisés dans la coulée sous pression en chambre froide
Le procédé de moulage sous pression en chambre froide convient aux métaux ayant un point de fusion élevé. Il peut s’agir notamment de l’aluminium, du magnésium, du cuivre, etc. Il est donc important de connaître les propriétés des métaux avant de les choisir pour le moulage sous pression en chambre froide. Vous trouverez ci-dessous un tableau détaillé des métaux courants pour le moulage sous pression en chambre froide.
Métal | Densité (g/cm³) | Point de fusion (°C) | Caractéristiques principales | Applications typiques |
---|---|---|---|---|
Aluminium | 2.7 | 660 | Léger, bonne résistance à la corrosion, conducteur | Pièces automobiles, composants aérospatiaux, biens de consommation |
Magnésium | 1,74 | 650 | Très léger, excellent rapport résistance/poids | Composants structurels légers, aéronautique, électronique |
Cuivre | 8,96 | 1085 | Conductivité thermique élevée, résistant à la corrosion, solide | Composants électriques, dissipateurs thermiques, roulements à haute charge |
Quels sont les avantages du moulage sous pression en chambre froide ?
Le procédé de moulage sous pression en chambre froide est particulièrement adapté à la production de pièces à partir de métaux à point de fusion élevé et offre plusieurs avantages significatifs. Voici cinq avantages principaux :
- Pièces moulées solides et durables : le moulage sous pression en chambre froide produit des pièces d’une résistance et d’une durabilité exceptionnelles, grâce à la haute pression utilisée pendant le processus de moulage. Le métal est forcé dans des moules complexes en utilisant cette méthode sous une pression immense afin d’obtenir des pièces moulées microstructurées denses avec de meilleures propriétés mécaniques que celles créées par moulage à la cire perdue ou par moulage sous pression par gravité .
- Excellente précision dimensionnelle : Grâce à la haute précision du moule moulé sous pression et au processus de production spécial, les pièces fabriquées à partir du processus de moulage sous pression en chambre froide présentent une grande précision dimensionnelle et une grande stabilité. Les caractéristiques rendent le moulage sous pression en chambre froide adapté à la production de formes complexes nécessitant des tolérances serrées pour de larges applications.
- Parois plus fines : en appliquant une pression élevée, le moulage sous pression en chambre froide est capable de créer des pièces moulées complexes avec des parois minces, tout en conservant une bonne résistance et de bonnes propriétés.
- Finition de surface lisse : le procédé permet de produire des composants aux surfaces lisses ne nécessitant que peu ou pas d’étapes de finition. Il peut contribuer à réduire les opérations secondaires telles que l’usinage et le polissage, ce qui permet d’économiser du temps et de l’argent dans les processus de fabrication.
- Taux de production rapides : Bien que les temps de cycle pour le moulage sous pression en chambre froide ne soient pas aussi rapides que ceux du moulage sous pression en chambre chaude, car le métal doit y être introduit manuellement à la louche à partir de son processus de fusion, cela permet toujours des taux de production relativement rapides et est particulièrement important lorsqu’il s’agit de processus de fabrication à grande échelle.
Quels sont les inconvénients du moulage sous pression en chambre froide ?
Bien que le moulage sous pression en chambre froide présente de nombreux avantages, il présente également quelques inconvénients, notamment par rapport à d’autres procédés de moulage tels que le moulage sous pression en chambre chaude. Voici trois inconvénients majeurs :
- Coûts opérationnels plus élevés : le moulage sous pression en chambre froide nécessite un équipement séparé pour faire fondre le métal et une manipulation supplémentaire, ce qui augmente les coûts de fabrication.
- Limité aux métaux à point de fusion élevé : le moulage sous pression en chambre froide ne convient pas à tous les métaux moulés sous pression. Il convient uniquement aux métaux à point de fusion élevé, tels que les alliages d’aluminium et de cuivre. Pour les métaux à point de fusion inférieur, le moulage sous pression en chambre chaude est le bon procédé à sélectionner.
Différences entre le moulage sous pression en chambre chaude et le moulage sous pression en chambre froide
Fonctionnalité | Coulée sous pression en chambre chaude | Moulage sous pression en chambre froide |
Approvisionnement en métal fondu | Le four relié directement à la machine | Du métal est versé dans la chambre |
Taille de la machine | Machines plus petites | Machines plus grandes |
Durée du cycle | Plus court en raison de l’accès immédiat au métal en fusion | Plus long en raison du limage du métal |
Compatibilité des métaux | Convient aux alliages à bas point de fusion comme le zinc, l’étain et le plomb | Gamme plus large comprenant des alliages d’aluminium, de magnésium et de cuivre |
Entretien | Plus fréquent en raison de l’exposition à des températures élevées | C’est moins fréquent car la machine ne touche pas le métal en fusion |
Investissement initial | Moins élevé en raison de machines plus petites et de configurations plus simples | Plus élevé en raison de machines plus grandes et d’équipements supplémentaires |
La vie meurt | Durée de vie plus courte en raison de l’exposition à des températures élevées et au métal en fusion | Durée de vie plus longue car aucun contact direct avec le métal en fusion |
Apprenez-en davantage sur les différences entre le moulage sous pression en chambre chaude et le moulage sous pression en chambre froide …
Applications du moulage sous pression en chambre froide
- Industrie automobile : les pièces automobiles nécessitent des métaux ayant des points de fusion élevés. Le choix du moulage sous pression en chambre froide est une bonne option. Il peut être utilisé dans la fabrication de composants de moteur, de pièces de transmission et de composants de structure. Il bénéficie donc de rapports résistance/poids élevés. De plus, il offre la précision des pièces moulées sous pression en chambre froide.
- Industries aérospatiales : Il a de nombreuses applications dans la fabrication de composants aéronautiques. Il peut inclure la fabrication de boîtiers, de supports et de pièces structurelles. Ces pièces sont légères et très résistantes. Ainsi, le moulage sous pression en chambre froide peut les traiter avec précision.
- Électronique : L’industrie électronique utilise d’autres matériaux à conductivité thermique et électrique élevée. Dans ce cas, le moulage sous pression en chambre froide joue un rôle important dans le traitement des matériaux à point de fusion élevé. Il peut être utilisé dans les dissipateurs thermiques et autres composants électroniques. Il offre les avantages d’une excellente conductivité thermique et d’une précision dimensionnelle des pièces électroniques.
- Biens de consommation : Il a également de nombreuses applications dans les biens de consommation. Il est utilisé pour la production de biens tels que des appareils électroménagers, des outils électriques et du matériel informatique. C’est donc une solution assez efficace, car des composants durables et conçus avec précision sont nécessaires.
Télécommunications : L’industrie des télécommunications utilise largement des matériaux comme l’aluminium et le cuivre. Il joue donc un rôle assez important dans la fabrication des composants des télécommunications, c’est-à-dire des boîtiers d’antenne et des supports de montage.
Questions fréquemment posées
Q1. Quels métaux peuvent être utilisés dans la coulée sous pression en chambre froide ?
Vous pouvez utiliser plusieurs métaux à point de fusion élevé comme l’aluminium, le magnésium et le cuivre. Ces métaux ont une durabilité supplémentaire, une excellente résistance et une résistance au chlore. Ce sont donc des fournisseurs d’applications idéaux.
Q2. Quelles alternatives pouvez-vous utiliser pour le moulage sous pression en chambre froide ?
Étant donné que le moulage sous pression en chambre froide présente certaines limites, il existe plusieurs alternatives que vous pouvez utiliser. Cela comprend le moulage sous pression en chambre chaude pour les métaux à bas point de fusion. Vous pouvez utiliser le moulage par cire perdue pour la fabrication de pièces complexes et très efficaces. De plus, le moulage au sable peut être utilisé pour des pièces de grande taille et complexes dans une variété de métaux.
Contactez Be-Cu.com pour des services de moulage sous pression en chambre froide
Be-Cu.com est une entreprise professionnelle de moulage sous pression en Chine. Nous avons de nombreuses années d’expérience dans le domaine du moulage sous pression et exportons des pièces moulées sous pression vers les marchés étrangers depuis 2008. Nous produisons principalement des pièces moulées sous pression en aluminium de haute qualité par le procédé de moulage sous pression en chambre froide.
Alors, si vous recherchez des services de moulage sous pression en chambre froide, contactez Be-Cu.com pour obtenir un devis instantané pour votre source unique. Nous serons toujours là pour vous servir !